Como líder mundial no mercado de compostos farmacêuticos, a Fagron aplica uma rigorosa política de qualidade e segurança do produto. Se um produto não atender a todas as especificações de qualidade, poderá causar efeitos colaterais nos usuários finais. Por isso, a qualidade e a segurança do produto são prioridade para a Fagron.
Metas e objetivos
Nosso objetivo é fornecer produtos que atendam a todos os requisitos de qualidade e segurança do produto. Um bom indicador dessa meta é o número de recalls de produtos em um ano. Em alguns casos excepcionais, os produtos devem ser recolhidos porque não atendem a todas as especificações de qualidade. Dividimos o recall de produtos em três categorias.
- A classe 1 diz respeito a um recall de produtos que podem causar ferimentos graves;
- A classe 2 diz respeito a recalls de produtos que podem causar efeitos colaterais temporários;
- A classe 3 diz respeito a produtos que provavelmente não causam ferimentos ou doenças, mas não atendem (totalmente) aos padrões GMP/BPF (boas praticas de fabricação).
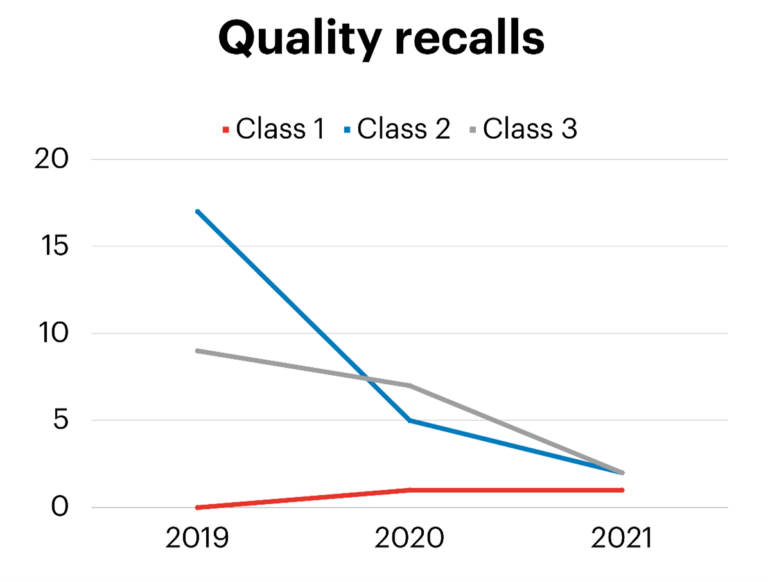
Processo de qualidade da Fagron
Procedimento de seleção de fornecedores
Um amplo processo de seleção de fornecedores garante a rastreabilidade das mais de 2.500 matérias-primas farmacêuticas utilizadas pela Fagron. Novos fornecedores são examinados extensivamente. Documentos de qualidade e documentos de fabricação são salvos com a ajuda de um aplicativo de software acessível a todas as empresas do Grupo Fagron. Fornecedores de produtos com maior perfil de risco são submetidos a auditoria in loco. Essas auditorias se concentram principalmente na qualidade e segurança do produto.
Produtos recebidos
Todas as matérias-primas farmacêuticas que chegam a um de nossos locais de composição e reembalagem, são testadas por técnicos de qualidade para garantir que atendam a todas as leis e regulamentos, requisitos e padrões internos aplicáveis.
Manufatura
A Fagron possui 34 instalações de composição e reembalagem em todo o mundo (2021) que cumprem totalmente a BPF (Boas Práticas de Fabricação) ou leis locais equivalentes. Trata-se de uma combinação de instalações certificadas e instalações onde uma auditoria é realizada regularmente pelas autoridades pelos padrões e legislação GMP/BPF.
Certificações internacionais como GMP e GDP exigem que todos os funcionários que tenham contato com produtos farmacêuticos participem de vários treinamentos anuais sobre qualidade e segurança do produto. O treinamento sobre procedimentos operacionais padrão (SOPs) na maioria de nossas instalações de reembalagem e produção estéril ocorre por meio do software MasterControl. A cada mês, mais de 7.000 tarefas de treinamento são concluídas. Cada usuário, em média, completa duas tarefas de treinamento por semana. Uma tarefa de treinamento poderia, por exemplo, aprender sobre um novo procedimento de limpeza de produtos antes de entrarem em um ambiente de produção limpo.
Produtos lançados
Os produtos finais em nossas instalações de manipulação estéreis e não estéreis são feitos por técnicos de qualidade para garantir que atendam a todas as especificações. A maioria (aproximadamente 2/3) dos produtos farmacêuticos que fornecemos de nossas instalações de reembalagem e compostos são testados internamente em um de nossos próprios laboratórios de qualidade antes de serem liberados; um terceiro (externo) testa o restante (aproximadamente 1/3).
Acompanhamento de ocorrências de qualidade
As ocorrências de qualidade na maioria das nossas instalações de reembalagem e produção estéril são registrados via MasterControl. Isso significa que temos uma visão geral clara de reclamações, recomendações de auditoria, desvios de procedimentos de qualidade e outras ocorrências. O processo de revisão de ocorrência e prevenção de ocorrências de qualidade no futuro também é rastreado no MasterControl.